Coating Thickness: The Limits of Thermal Spray Coatings
(Part 2 of 3)
People often assume that the thicker the coating, the better the performance; but this isn’t always the case. Thermal spray has its limitations; from geometrical limitations to coating thickness to the operating environment. Metallic alloys, cermets, and ceramic coatings have different limits for coating thickness. To better understand the thickness limitations of thermal spray we’ll look at why they exist, what variables contribute to them, and what they are.
Cermets: (n) materials that are comprised of metallic alloys and ceramic materials. i.e., tungsten carbide cobalt chrome or tungsten carbide nickel
Why Do Thickness Limits Exist for Thermal Spray?
Thermal spray coatings have thickness limitations because of the way the coatings are applied. All thermal spray processes involve heating up a coating material and propelling it to the part via a gas of some kind, forming splats of coating. These splats build up on the surface of the substrate, creating internal stresses between particles, which form the thermal spray coating. This unique way of coating can create very strong mechanical bonds but due to the internal stresses can only be built up so much. The amount it can build up depends largely on the coating material and the thermal spray process.

What Determines the Thickness Limits of Thermal Spray Coatings?
The coating material is the primary factor in determining the coating thickness limit. In general, the harder the coating is the greater the limitation. The ductility of the coating is determined by the atomic structure of the elements that make up the material as well as the internal stresses between splats during coating application. There’s more science there on the modulus of elasticity and metals versus ceramics but we’ll save that for another time. Essentially metal alloys are more ductile and can therefore be applied at greater thickness. On the other end of the spectrum are ceramics which are very hard but brittle at greater thickness. Somewhere in between we find cermets, like tungsten carbide, which combine metallic alloys with ceramics to create a more ductile yet hard coating.
Another element of thickness limits is the thermal spray process. Each process uses different methods to heat up the coating material and propel the particles to the part. These factors cause differing limitations among the processes. Some processes, like HVAF thermal spray, are specially engineered to heat the coating particles in such a way as to increase the ductility of the coating. This means that even though HVOF and HVAF are similar processes that typically apply similar materials, HVAF coatings can be built up thicker than HVOF. Coating thickness limits can sometimes be altered by adjusting the spray parameters, but only so much. These variables, along with the coating material selection, will determine the coating thickness limits.
What are the Thickness Limits of Thermal Spray Coatings?
The thermal spray coating material often dictates which type of thermal spray process you can use. Some materials can be applied with more than one process to produce variations in the coating while others can only be applied with one process. Arc and flame thermal spray coatings are typically metallic alloys so they can be built up thicker without many issues; usually up to around 0.25” depending upon the exact material. This makes them great for dimensional restoration.
Cermets, carbides, and ceramics, usually applied with HVOF or plasma can build up to 0.020” thick. Some metallic alloys can be applied with these processes as well and then their thickness limit is dictated by the spray process. There can be exceptions to this rule depending on the thermal spray process and material. High Velocity Air Fuel thermal spray, or HVAF thermal spray, can sometimes be applied up to 0.050” thick or more. For most materials, coatings do not need to be applied at the full thickness limitation to achieve optimum wear and corrosion resistance.
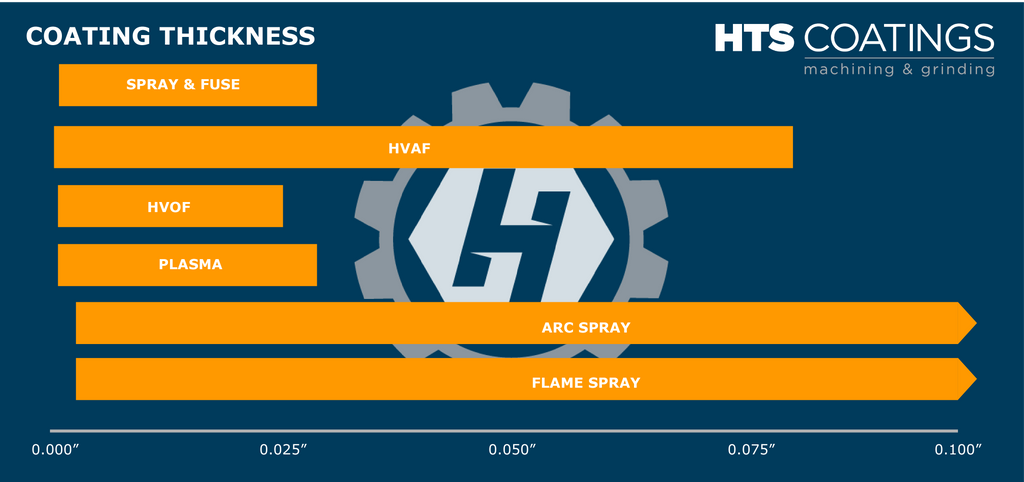
When to Watch Out
Depending on your coating needs, coating thickness may limit what material or spray process you can use. Most coatings don’t need to be applied as thick as their limit and offer full performance at a fraction of them. The most common scenario that is impacted by coating thickness is the remanufacture of worn parts. When the damage is too deep then a welded or spray and fused coating may be the better choice. Sometimes the damaged areas can be patch-welded before applying a thermal spray coating if the damage is localized to small areas. This will depend on the base material and economic feasibility. If you are unsure if you will run into coating thickness limitations or if want to know if there is a way around them in your situation the best thing to do is to consult with a knowledgeable thermal spray provider who can suggest the right coating or other solution, if necessary.
- Choosing a selection results in a full page refresh.
- Press the space key then arrow keys to make a selection.